Have you ever wondered where DC motors are used? Well, they’re actually pretty versatile and can be found in all sorts of things like cars, appliances and even industrial equipment.
There are actually several different types of DC motors out there, each with its own pros and cons that make them better suited for certain applications.
Whether you’re an engineer, a mechanic or just someone who’s curious about motors, this article is full of valuable information that will give you a solid overview of these amazing machines.
What is DC motor?
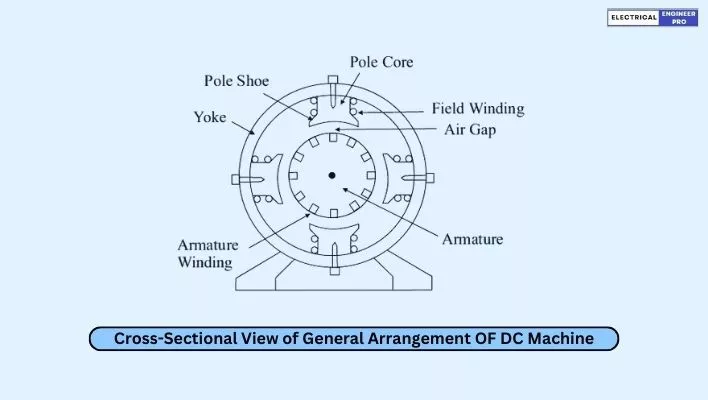
A DC motor is a special type of electrical machine that converts electrical energy or power from a direct current (DC) source into mechanical energy or power. In other words, it transforms electricity into motion. It does this by utilizing the interaction between magnetic fields and electric currents.
DC motors are widely used in various applications, ranging from small household appliances to large industrial machinery. Their ability to provide precise control over speed and direction makes them suitable for a wide range of tasks, such as driving conveyor belts, powering electric vehicles, operating robotic arms, and much more.
Also Read: Electrical Machines | Discover the Basics
What is the basic working principle of DC Motor?
To generate a force on a conductor, we require two specific conditions:
- The conductor must have electric current flowing through it.
- The conductor must be positioned inside a magnetic field.
When these two conditions are fulfilled, a force is exerted on the conductor, causing it to try and move in a direction that is perpendicular to the magnetic field. This fundamental theory forms the basis for the operation of all DC motors.
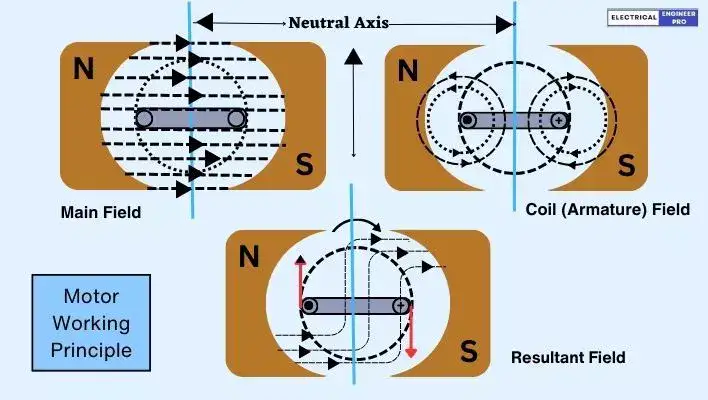
Let’s break down the process of how a DC motor works with just one coil of the armature and a two-pole machine:
- Magnetic Field Creation: In a two-pole machine, there are two main poles, each generating its own magnetic field called main field.
- Coil and Current Flow: The single coil of the armature is placed within the main magnetic field of a two-pole machine, and is connected to a DC power source. Once the DC power supply is connected to the coil, electric current starts flowing through it.
- Coil’s Magnetic Field: As current flows through the coil, it generates its own magnetic field around it, called Armature field. This field interacts with the machine’s main magnetic field.
- Resultant Field: The interaction between the magnetic fields of the main poles and the coil (armature) leads to the formation of a resultant magnetic field.
- Seeking Equilibrium: The resultant magnetic field has a natural tendency to align itself with the original position, i.e., in a straight line.
- Force and Torque: As the resultant field tries to return to its original position, it exerts a force on the two sides of the coil. This force causes a twisting motion, known as torque, to develop in the coil.
- Coil Rotation: The torque produced in the coil causes it to start rotating within the magnetic field.
In summary, when we apply a DC power supply to the coil of the armature in a two pole machine, it creates a magnetic field around the coil. The interaction between this coil’s field and the main poles’ field generates a resultant field that seeks to come back to its original alignment. This seeking action exerts a force on the coil, causing torque to develop, which ultimately rotates the coil. This rotation is the fundamental principle behind the operation of a DC motor.
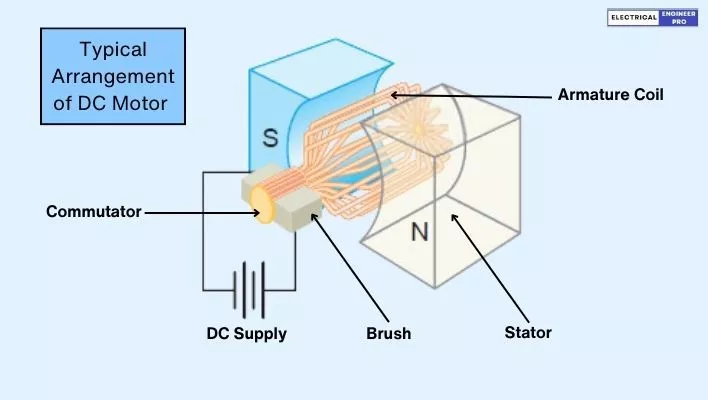
In a real DC motor, there are many coils (conductors) arranged on the armature. The conductors located under the influence of the North pole carry the current outward, while the conductors affected by the South pole carry the current in the opposite direction. This arrangement creates a resultant rotor field, as shown in the Figure.
This resultant rotor field tries to align itself with the main field, which is the magnetic field created by the stator. As a result of this alignment attempt, a twisting force known as torque develops. This torque causes the rotor (the armature) to rotate. This rotation is how the DC motor operates, and it’s the reason why the armature turns and the motor functions as intended.
To ensure a consistent torque, it is necessary to reverse the direction of current flow in each conductor or coil side as it crosses the magnetic neutral axis (MNA). This reversal is accomplished through the use of a commutator.
Types of DC motors
DC motors are divided into separately excited, self-excited, and permanent magnet motors. Here, our focus will center on self-excited and permanent magnet motors, delving into their unique features and applications.
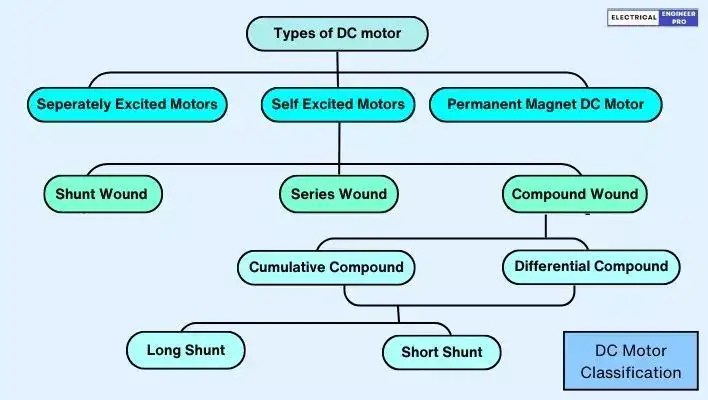
DC series motor
A DC series motor is a type of direct current (DC) motor in which the field winding and the armature winding are connected in series. This means that the same electric current flows through both the field winding (located on the stator) and the armature winding (located on the rotor) when the motor is operating.
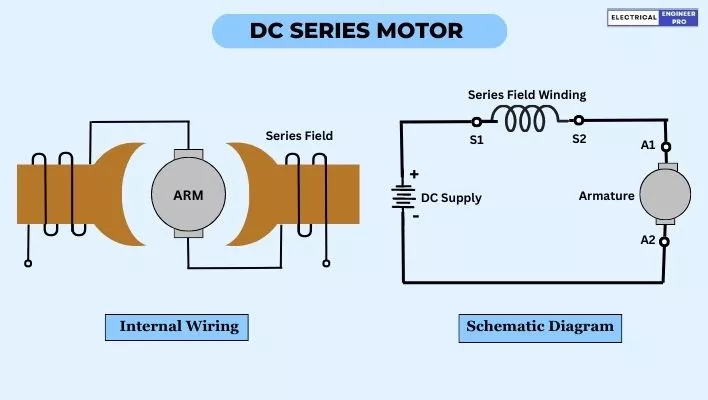
Key features of a DC series motor
- High Starting Torque: DC series motors offer high starting torque, but speed decreases as torque and armature current increase. Perfect for applications needing strong starting torque for slow movement of heavy loads and faster movement of lighter loads, such as electric traction, cranes, and hoists.
- Variable Speed Control: The series motor is a variable speed motor, meaning its speed adjusts with changes in armature current or load. When the load reduces, the motor’s speed increases accordingly.
- Strong Magnetic Field: A series motor has a low resistance field and low resistance armature circuit, which results in a strong magnetic field when voltage is applied. Thus contributing to the motor’s high starting torque.
- Self-Excitation: DC series motors are self-excited, meaning they generate their own magnetic field without the need for a separate excitation source.
- Speed-Torque Characteristics: The speed-torque characteristics of a DC series motor show that as the load increases, the speed decreases and vice versa. This means that the speed decreases significantly under heavy loads, which can be both an advantage and a limitation depending on the application.
- No constant speed: In this type of motor speed varies widely between no load and rated load. Therefore, these motors cannot be used where a constant speed is required with variable loads.
- High Current Draw: One drawback of DC series motors is that they draw a high current, which can lead to efficiency and heating issues if not managed properly.
Applications of DC series motor
- Electric Traction: DC series motors are widely used in electric locomotives, trains and trams due to their ability to provide high starting torque and efficient speed control, making them suitable for transportation systems.
- Cranes and Hoists: DC series motors are commonly used in cranes, hoists, and elevators where high starting torque is required to lift heavy loads.
- Electric Forklifts: DC series motors are used in electric forklifts because they offer excellent starting torque for moving heavy loads and precise speed control for maneuverability.
- Electric Winches: DC series motors are employed in electric winches for their high torque output, making them suitable for pulling heavy loads.
- Air Compressors: In some air compressors DC series motors are used for their high starting torque and efficient operation.
- Electric Fans: Some electric fans, particularly those used in industrial settings, use DC series motors for their high torque and variable speed control features.
DC shunt motor
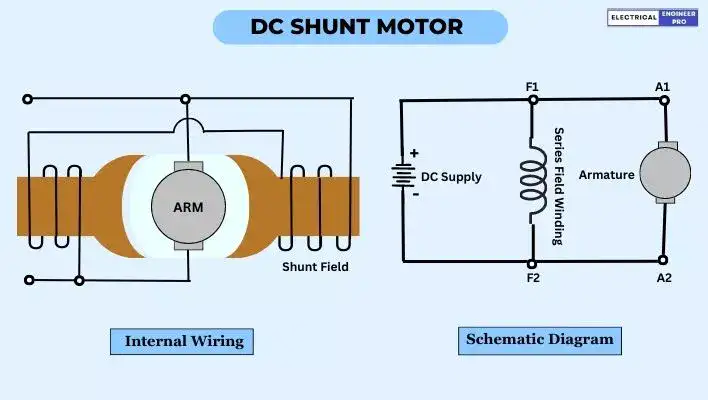
A DC shunt motor is a type of direct current (DC) motor where the field winding and the armature winding are connected in parallel, or “shunt.” This means the voltage across the field winding is equal to the voltage across the armature.
The field winding has high resistance and is constructed with multiple turns of small-gauge wire and has lower current flow compared to DC series motors.
The power supply for the DC shunt motor is directly connected to the field winding, which keeps the current constant in the field. Unlike DC series motors, the field current doesn’t change with the motor’s speed.
This means that the torque relies only on the current in the armature. When starting, the motor has low torque because of its slow speed, but as it reaches its full speed, it achieves its highest torque.
Key features of a DC shunt motor
- Stable Speed Regulation: DC shunt motors offer relatively constant speed regulation over a wide range of loads, making them suitable for applications requiring consistent speed.
- Separate Field and Armature Windings: The motor has two separate windings: one for the field (shunt winding) and one for the armature, which allows independent control of field and armature currents.
- High resistance shunt winding: The shunt field winding has high resistance and is constructed with multiple turns of small-gauge wire and has lower current flow compared to DC series motors.
- Medium Starting Torque: DC shunt motors provide moderate starting torque, making them suitable for applications where a smooth and controlled start is required.
- No starting on heavy load: A large armature current is required at the start if the machine is on heavy load. Thus, the shunt motor should never be started on load.
- Speed Control: There are two techniques to control the speed of a DC shunt motor:
- Changing the total amount of current flowing through the shunt windings.
- Changing the total amount of current flowing through the armature.
- Self-Excitation: DC shunt motors are self-excited, meaning they do not require a separate excitation source to generate the magnetic field.
- Regenerative Braking: These motors can be used for regenerative braking, where energy is recovered during deceleration and returned to the power supply.
- Suitable for Constant Speed Applications: DC shunt motors are well-suited for applications that require a relatively constant speed under varying loads.
- Low Starting Current: They draw low starting current, reducing the risk of electrical overload during motor start-up.
Applications of a DC shunt motor
DC shunt motors find a wide range of applications in various industries and devices due to their specific characteristics. Some common applications of DC shunt motors include:
- Machine Tools: DC shunt motors are used in machine tools such as lathes, milling machines and drilling machines, where precise and constant speed control is essential for accurate machining operations.
- Conveyors: DC shunt motors are employed in conveyor systems to move materials smoothly and continuously at a constant speed.
- Pumps and Fans: DC shunt motors are used in pumps and fans for their ability to maintain a constant speed, ensuring efficient fluid flow and airflow.
- Printing Presses: DC shunt motors are used in printing presses to control the speed of the printing rolls and maintain uniform printing quality.
- Elevators and Lifts: DC shunt motors are utilized in elevators and lifts for their constant speed characteristics, providing smooth and controlled vertical transportation.
- Blowers and Compressors: DC shunt motors are used in blowers and compressors for their ability to maintain a consistent airflow and pressure.
- Battery-Powered Vehicles: Some battery-operated vehicles, like electric golf carts and electric boats, use DC shunt motors for their constant speed control and efficiency.
- Centrifugal Pumps: DC shunt motors are employed in centrifugal pumps to maintain a steady rotational speed, ensuring consistent fluid pumping.
- Electric Hoists and Cranes: DC shunt motors are used in electric hoists and cranes for their ability to provide precise speed control and lift heavy loads.
- Generators: In some cases, DC shunt motors can be used as generators in applications where they need to convert mechanical energy into electrical energy.
Compound DC motors
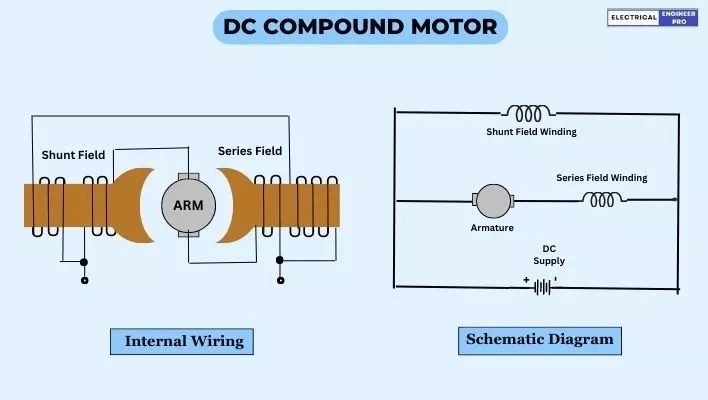
A DC compound motor, also known as a compound-wound DC motor, is a type of direct current (DC) motor that combines the characteristics of both series-wound and shunt-wound DC motors. In a DC compound motor, both the series winding and the shunt winding are connected in parallel, or “compound,” to the armature.
Key features of a DC compound motor
- Series Winding: The series winding is connected in series with the armature winding, which means the same current flows through both windings. This arrangement provides the motor with a high starting torque, similar to series-wound DC motors.
- Shunt Winding: The shunt winding is connected in parallel with the armature winding, and it receives a constant or nearly constant voltage supply. This creates a steady magnetic field in the motor, similar to shunt-wound DC motors.
- There are two main types of DC compound motors based on the arrangement of their series and shunt windings:
- Cumulative Compound Motor: In this type, the series winding adds to the magnetic field produced by the shunt winding. As a result, the cumulative compound motor exhibits a higher torque than the shunt motor at all speeds. It provides excellent starting torque and good speed regulation.
- Differential Compound Motor: In this type, the series winding opposes the magnetic field produced by the shunt winding. As a result, the differential compound motor exhibits reduced torque as the speed increases, making it suitable for applications where the load decreases with speed.
- High Starting Torque: Similar to series-wound DC motors, compound motors provide high starting torque. The series winding, being in series with the armature, contributes to the strong starting torque, making the motor suitable for applications that require the ability to start under heavy loads.
- Constant Speed Regulation: Like shunt-wound DC motors, compound motors offer good speed regulation. The shunt winding, connected in parallel with the armature, creates a steady magnetic field, helping maintain a relatively constant speed even with varying loads.
- Speed-Torque Characteristics: The speed-torque characteristics of compound motors depend on the specific type (cumulative or differential) and can be tailored to suit the requirements of different applications.
- Efficient Speed Control: Compound motors can be controlled effectively by adjusting the voltage applied to the shunt winding, allowing precise and smooth speed control for various operating conditions.
- Reliable and Durable: DC compound motors are known for their reliability and durability. With proper maintenance and care, they can have a long operational life, making them cost-effective solutions for industrial applications.
Applications DC compound motor
Compound motors are preferred in various applications due to their specific characteristics, which allow them to perform exceptionally well under certain conditions. Here’s an explanation of why Compound motors are used in specific industries:
- Elevators: Compound motors are used in elevators because of their ability to handle heavy load changes effectively. Elevators often need to lift and lower varying weights of passengers and cargo, and compound motors provide the necessary high starting torque and speed control to ensure smooth and safe vertical transportation.
- Shears and Punches: In shears and punch machines, compound motors are utilized because of their high starting torque and superior speed control. These machines require precise control and power to cut and shape materials, and compound motors meet these requirements effectively.
- Steel Rolling Mills: Compound motors are well-suited for steel rolling mills due to their high starting torque and ability to handle heavy-duty loads. Steel rolling mills involve the continuous rolling of metal, which demands motors capable of maintaining steady speed and torque during the rolling process.
- Printing Press and Cutting Machines: The printing press and cutting machines benefit from compound motors’ capacity to drive heavy loads efficiently. The printing process requires consistent speed for accurate prints, while cutting machines need power to cut through various materials, and compound motors provide the necessary strength and speed control.
- Stamping Presses: Stamping presses use compound motors to achieve high starting torque, which is crucial for stamping operations where precision and force are needed to create intricate shapes and patterns.
- Mixers: Mixers require good speed control and high starting torque to blend materials effectively. Compound motors provide these features, making them a great choice for mixers used in various industries, such as food processing and chemical manufacturing.
In summary, Compound motors are selected for specific applications based on their high starting torque, efficient speed control, and ability to handle heavy loads. These characteristics make them suitable for elevators, shears, steel rolling mills, printing presses, cutting machines, stamping presses, mixers, and other applications that demand reliable and robust motor performance.
PMDC motor
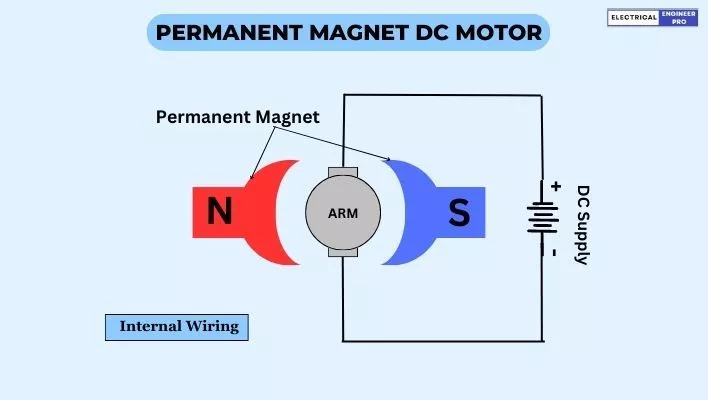
Motors generate a rotating magnetic field by employing coils and field currents. However, this construction has some drawbacks which include high energy consumption, heat generation and the need for large motor sizes due to the presence of field poles.
So to overcome these downsides PMDC (Permanent Magnet DC) motors use permanent magnets instead of field coils. This makes the motors smaller, more efficient and eliminates the risk of losing control due to field failure.
Key features of a PMDC motor
- Permanent Magnets: A PMDC motor has fixed permanent magnets, usually made of materials like neodymium or ferrite, placed on the stator. These magnets create a fixed magnetic field in the motor.
- Armature with Windings: The armature, the rotating part of the motor, consists of a core made of soft iron and a coil of wire (windings) wound around it. The armature windings are typically made of copper wire and are connected to a commutator.
- Commutator: The commutator is a rotary switch connected to the armature windings. As the armature rotates, the commutator ensures that the current direction in the armature windings changes at the right moments to maintain continuous rotation.
- Brush Contacts: The commutator connects to stationary brushes that maintain electrical contact with the commutator segments. These brushes are typically made of carbon or graphite, providing a low-friction electrical connection.
- Electric Current Flow: When a direct current (DC) is supplied to the armature windings, an electric current flows through them. This electric current interacts with the magnetic field generated by the permanent magnets.
- Magnetic Field Interaction: The interaction between the magnetic field of the permanent magnets and the armature’s magnetic field, induced by the electric current, creates a force known as torque.
- Torque and Rotation: The torque exerts a twisting force on the armature, causing it to rotate. The rotation continues as long as the electric current flows through the armature windings and the magnetic interaction persists.
- Speed and Direction Control: By adjusting the amount and direction of the electric current supplied to the armature windings, the speed and direction of the PMDC motor’s rotation can be controlled.
Advantages of PMDC Motors
- No Field Winding: PMDC motors don’t use field winding, which means there is no copper losses in the field circuit.
- Better Efficiency: PMDC motors are super efficient because they don’t lose any electrical power while creating the magnetic field. The magnetic field is naturally generated by a permanent magnet, which is essential for the motor to work. This makes PMDC motors very efficient in their operation.
- Smaller and Compact: PMDC motors are smaller in size because they don’t have field winding.
- No Extra Setup: PMDC motors use special magnets to create the magnetic field, thus eliminating the need for a field excitation arrangement
- Cost-Effective: PMDC motors are cheaper, especially for applications that need less power. They are a cost-effective choice.
Disadvantages of PMDC Motors
The disadvantages of Permanent Magnet DC (PMDC) motors are as follows:
- Limited Flux Density: The permanent magnets used in PMDC motors cannot generate high flux density, resulting in a smaller electromagnetic torque per ampere of current.
- Risk of Demagnetization: PMDC motors face a risk of demagnetization of the magnetic poles, especially when subjected to large armature currents or prolonged overloading, leading to a loss of magnetic strength.
- Constant Magnetic Field: The magnetic field in a PMDC motor is present continuously, even when the motor is not in use. To prevent any harm to the motor, it should be fully enclosed to avoid attracting foreign magnetic materials to the permanent magnets.
- Uncompensated Armature Reaction: PMDC motors have difficulty compensating for the armature reaction, potentially weakening the magnetic field due to its demagnetizing effect.
- Fixed Field Flux: The field flux in a PMDC motor remains fixed, making it challenging to control the motor’s speed. Unlike other motor types, adjusting the field flux is not easily achievable in PMDC motors, limiting their speed control capabilities.
Applications of PMDC Motors
PMDC motors find a wide range of applications in various industries and devices due to their advantages and characteristics. Some common applications of PMDC motors include:
- Electric Vehicles: PMDC motors are used in electric scooters, bicycles and small electric cars due to their high starting torque and efficient speed control.
- Home Appliances: PMDC motors are found in household appliances such as vacuum cleaners, blenders, mixers, and fans, where precise speed control and compact size are essential.
- Power Tools: Drills, grinders, saws, and other power tools often use PMDC motors for their high starting torque and efficient power delivery.
- Robotics: PMDC motors are employed in various robotic applications, including robotic arms, automated manufacturing, and autonomous vehicles.
- Medical Devices: Some medical equipment, like portable oxygen concentrators and infusion pumps, use PMDC motors due to their compact size and efficient energy usage.
- Aerospace: PMDC motors are used in small aircraft and unmanned aerial vehicles (UAVs) for their lightweight design and efficient power output.
- Entertainment Systems: PMDC motors are used in turntables and record players to drive the platter and control rotational speed.
- Electric Toys: Many battery-powered toys like remote-controlled cars, boats, and helicopters use PMDC motors for their compact size and efficient operation.
- Cooling Fans: PMDC motors are used in cooling fans for computers, electronics, and household appliances due to their low noise and efficient performance.
Also read: Electrical Transformers | A Deep Dive into its Mechanics
Summary of DC motors
Motor Types | Key Features | Applications | Power Range |
PMDC Motors | 1. Fixed permanent magnet instead of stator field coils. 2. Higher efficiency. 3. Smaller & Compact. 4. Can get demagnetized if used excessively. 5. Low torque | 1. Used in electric scooters, bicycles, and small electric cars. 2. Computer peripherals. 3. Home appliances like vacuum cleaners, blenders, mixers, and fans. 4. Robotic Applications | Up to 10 HP |
DC Series Motor | 1. Generates dangerously high torques at low speeds. Hence should be always connected to load. 2. Variable speed motor. 3. Cannot be used at constant speed with variable loads. | 1. Electric Traction. 2. Cranes and Hoists 3. Electric Forklifts 4. Elevators 5. Conveyors | Up to 200 HP |
DC Shunt Motor | 1. Has two separate windings: one for the field (shunt winding) and one for the armature. 2. Stable and consistent speed. 3. Moderate starting torque. 4. Motor should never be started on load. | 1. Used in regenerative braking. 2. Machine tools like lathes, milling machines and drilling machines. 3. Employed in centrifugal pumps. 4. Electric Hoists and Cranes | Up to 200 HP |
DC Compound Motor | 1. Has characteristics of both series-wound and shunt-wound DC motors. 2. High Starting Torque 3. Constant Speed Regulation 4. Efficient Speed Control | 1. Elevators 2. Shears and punch machines. 3. Steel Rolling Mills 4. Printing Press | Up to 200 HP |